In the world of fluid transfer systems, quick couplings play a pivotal role in ensuring efficient and leak-free connections. A critical component of these couplings is the seal ring, which ensures a tight seal and prevents leaks. Selecting the appropriate seal ring material is crucial for the performance and longevity of the quick couplings. In this blog post, we will delve into the various seal ring materials used in quick couplings and their respective advantages.
The Importance of Seal Rings
Seal rings are essential for maintaining the integrity of quick couplings. They provide a barrier that prevents fluid from escaping and contaminants from entering the system. The right seal ring material can enhance the durability, chemical resistance, and temperature tolerance of the coupling, making it suitable for a wide range of applications.
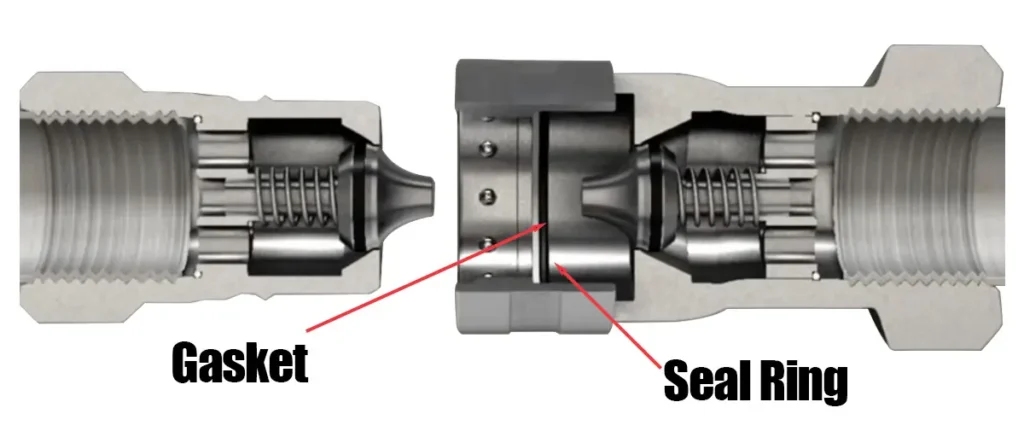
Common Seal Ring Materials
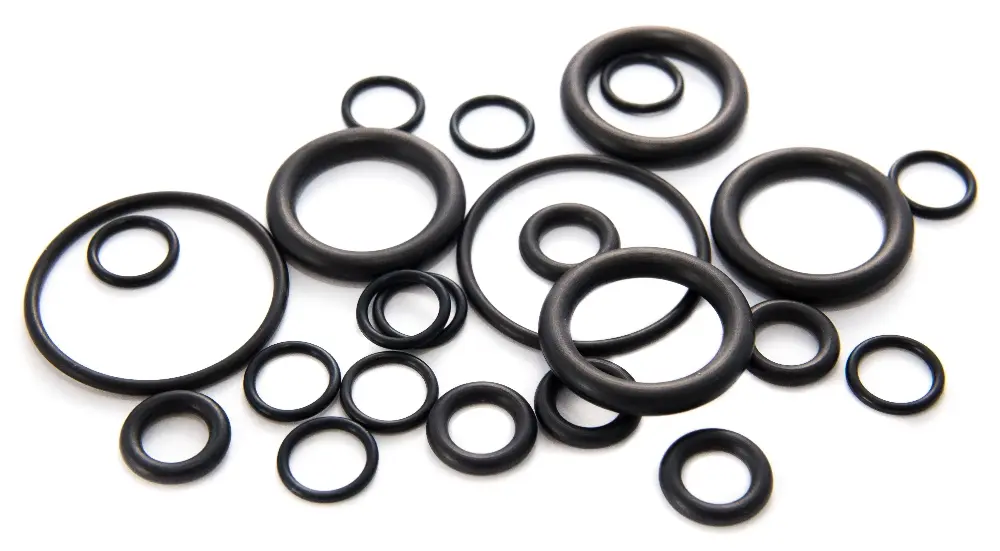
1.Nitrile Rubber (NBR)
Nitrile Rubber (NBR), also known as Buna-N or acrylonitrile butadiene rubber, is a synthetic rubber copolymer of acrylonitrile (ACN) and butadiene. It is renowned for its excellent resistance to oils, fuels, and other chemicals, making it a popular material in various industrial applications.
Properties of Nitrile Rubber (NBR)
- Oil and Chemical Resistance: NBR is highly resistant to petroleum-based oils and fuels, as well as many other chemicals. This makes it ideal for applications involving exposure to such substances.
- Temperature Range: NBR can typically operate within a temperature range of -40°C to 120°C (-40°F to 248°F). Some specialized grades can withstand even higher temperatures.
- Abrasion Resistance: NBR has good abrasion resistance, which contributes to its durability in demanding applications.
- Flexibility and Resilience: Despite its strength and resistance, NBR maintains a good level of flexibility and resilience, which is essential for sealing applications.
- Water Resistance: NBR also offers good resistance to water, which makes it useful in various sealing and gasket applications.
Nitrile Rubber (NBR) in quick couplings
Nitrile Rubber (NBR) is the sealing material used in most quick couplings. The fluid passing through most hydraulic quick couplings is hydraulic oil. Nitrile Rubber can be used in these applications. Compared with other sealing materials, Nitrile Rubber is relatively cheap and has better wear resistance. Therefore, Nitrile Rubber is the first choice for most quick coupling sealing materials. Most quick couplings, when customers do not have special requirements, almost all default to Nitrile seals.
Variations and Grades
NBR can be formulated in different grades to suit specific applications. Variations in the acrylonitrile content can adjust the balance between oil resistance and flexibility. Higher acrylonitrile content increases oil resistance but reduces flexibility, while lower acrylonitrile content enhances flexibility but decreases oil resistance.
Limitations of NBR
While NBR has many advantageous properties, it also has some limitations:
- Ozone and UV Resistance: NBR is not inherently resistant to ozone and UV light, which can cause it to degrade over time when exposed to outdoor environments. For quick couplings, this is usually not a big problem. Because the seal ring is usually installed inside the quick coupling. But this puts forward some requirements for the preservation of the seal rings. Do not store the seal in an area that is easily exposed to direct sunlight. At the same time, for hydraulic equipment used outdoors. When the quick coupling is disconnected, it is best to protect the quick connector with a dust cap. It also has a certain degree of protection for the seal.
- Temperature Extremes: Although it has a good temperature range, NBR is not suitable for extremely high or low temperatures compared to some other elastomers like silicone or fluorocarbon. Temperature is a particularly important factor in the selection of different sealing materials for quick connectors. When the operating temperature exceeds 100°C, we usually use FKM to replace NBR materials.
Nitrile Rubber (NBR) is a versatile and reliable material widely used in industries where resistance to oils, fuels, and chemicals is crucial. Its balance of properties makes it an ideal choice for most quick couplings used in lots of industries. By understanding its strengths and limitations, you can better appreciate why NBR is such a popular choice for seals, gaskets, hoses, and more.
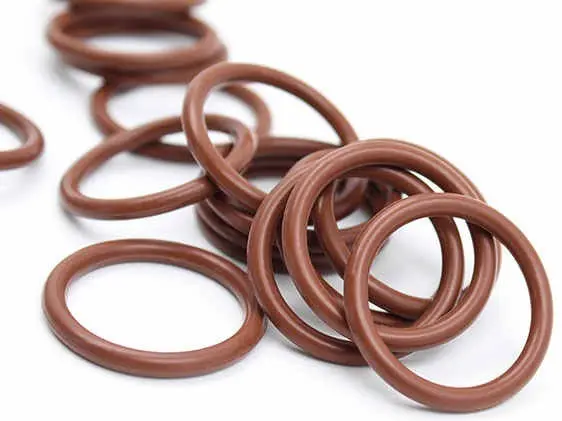
2.Viton® (FKM)
FKM is a type of synthetic rubber known as fluoroelastomer. This material is characterized by its high resistance to chemicals, heat, and oils, making it suitable for demanding applications. Viton® is a brand name of FKM, specifically produced by DuPont (now under Chemours). It is one of the most recognized and widely used brands of fluoroelastomers.
Properties of FKM
- Chemical Resistance: Excellent resistance to a wide range of chemicals, including hydrocarbons, acids, alkalis, and solvents. In most stainless steel quick couplings, we usually choose FKM seals. Because stainless steel quick couplings are usually used in applications where corrosive liquids are transported. FKM is corrosion resistant to most chemical liquids. In most cases, customers will not experience leakage due to purchasing the wrong seal material for quick connectors.
- Temperature Range: Capable of withstanding temperatures from -20°C to 200°C (-4°F to 392°F) and, in some formulations, even higher. Usually when the actual working temperature of quick couplings exceeds 100°C, we will recommend customers to use FKM material seals. For example, for some high-pressure hydraulic tool quick couplings, we will help customers replace the original NBR seals with FKM. and, for quick couplings used in the steam sterilization industry, we will replace them with FKM seals.
- Durability: High resistance to ozone, weathering, and aging, which enhances its longevity in harsh environments. Compared with NBR, FKM has a more stable performance. Therefore, in some applications, customers prefer to use FKM.
- Mechanical Properties: Good mechanical strength and flexibility, maintaining performance under high pressures and dynamic conditions.
Applications of FKM in quick couplings
- Automotive industry for seals, O-rings, and gaskets.
- Aerospace industry for fuel systems and hydraulic systems.
- Chemical processing for equipment that handles aggressive chemicals.
- Oil and gas industry for sealing components exposed to crude oil and other harsh substances.
In most of these applications, FKM seals are used together with stainless steel materials, thus ensuring that the quick couplings have very stable performance in these harsh environments.
Viton®
Viton® is a brand name of FKM, specifically produced by DuPont (now under Chemours). It is one of the most recognized and widely used brands of fluoroelastomers.
- Brand Assurance: As a branded product, Viton® is known for consistent quality and performance, meeting stringent industry standards.
- Chemical Compatibility:Viton® offers superior resistance to a broader range of chemicals, including aggressive fuels and acids.
- Temperature Stability: It can operate effectively in extreme temperatures, maintaining elasticity and mechanical properties.
- Grades of Viton®: Viton® is available in various grades tailored for specific applications.
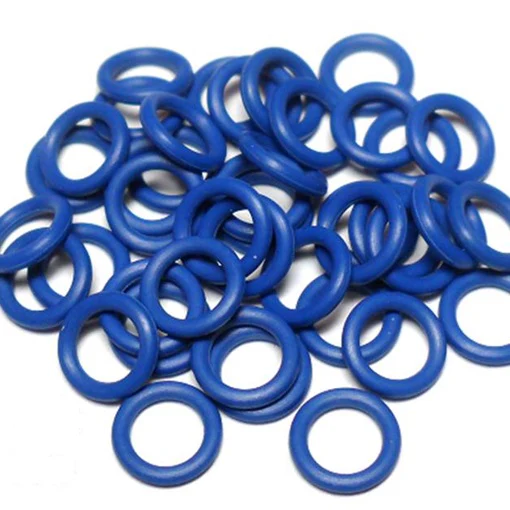
3.EPDM (Ethylene Propylene Diene Monomer)
EPDM (Ethylene Propylene Diene Monomer) is a type of synthetic rubber widely used for seal materials due to its excellent properties and versatility. EPDM is good water and steam resistance and is suitable for the food industry, it can be in contact with food and will not pollute. A large number of our customers are used in the food industry and can pass through water, steam and other applications.
Properties of EPDM
- Weather and Ozone Resistance: EPDM has outstanding resistance to ozone, UV rays, and weathering. This makes it highly suitable for outdoor applications where exposure to the elements is a concern.
- Temperature Range:It can operate effectively within a temperature range of -50°C to 150°C (-58°F to 302°F), making it suitable for both low and high-temperature environments.
- Water and Steam Resistance: EPDM offers excellent resistance to water and steam, making it ideal for applications involving water-based fluids and steam systems.
- Chemical Resistance: It has good resistance to a variety of chemicals, including many acids, alkalis, and polar solvents. However, it is not resistant to hydrocarbons, oils, and fuels.
- Flexibility and Elasticity:EPDM is known for its excellent flexibility and elasticity, which helps maintain a reliable seal under various mechanical stresses and movements.
- Electrical Insulation:EPDM is a good electrical insulator, which can be advantageous in applications requiring non-conductive materials.
Applications Of EPDM in Quick Couplings
- HVAC Systems: It is commonly used in HVAC systems for sealing ducts and as insulation material, thanks to its temperature tolerance and resistance to steam and water. The quick couplings used in air conditioners usually use this sealing material – EPDM. Domestic brands such as Midea and Gree will use quick connectors containing this material.
- Automotive Industry: EPDM is used for weatherstripping, seals, and gaskets in vehicles due to its durability and resistance to weather and temperature extremes. Some quick connectors used in automobile drainage systems are said to use this material. However, this type of quick connector is usually not processed with metal. So we have never come into contact with it. The material of this quick connector is plastic or nylon. This is beyond our manufacturing capacity.
- Water and Wastewater Systems: EPDM seals are utilized in plumbing and wastewater systems due to their resistance to water and various cleaning agents. Some of our Southeast Asian customers use brass or stainless steel quick connectors in their home water supply systems and they require this type of seal material.
- Industrial Applications: In industrial settings, EPDM is used for seals, gaskets, and hoses that need to withstand exposure to water, steam, and various chemicals.
Advantages of EPDM
- Longevity: EPDM seals have a long service life, even under harsh environmental conditions, due to their excellent weathering and aging resistance.
- Cost-Effective: EPDM is generally more affordable than other high-performance elastomers, offering a cost-effective solution for many sealing applications.
- Versatility: The material’s wide range of properties makes it suitable for diverse applications across different industries.
Limitations of EPDM
- Hydrocarbon Sensitivity: EPDM is not resistant to hydrocarbons, oils, and fuels. For applications involving these substances, other materials like NBR or FKM would be more appropriate. Therefore, we will not use EPDM as the default sealing material for common quick couplings. For most stainless steel quick couplings, we usually use FKM as the default sealing material. Only when customers know that EPDM can be used in their environment, will we change to EPDM material according to customer requirements. In fact, in many application scenarios, such as steam, water and other environments, EPDM performs better. This is to prevent customers from using quick connectors with EPDM seals in inappropriate environments. Relatively speaking, FKM has a wider range of applications.
- Mechanical Strength: While EPDM has good flexibility and resilience, it may not offer the same level of mechanical strength as some other elastomers, which can be a consideration in high-stress applications.
EPDM is a highly versatile and reliable seal material known for its excellent resistance to weathering, ozone, water, and steam. Its broad temperature range and chemical resistance (excluding hydrocarbons) make it suitable for a variety of applications, from automotive and HVAC systems to industrial and construction uses. In the quick coupling industry, because quick couplings are easily used by customers in hydraulic systems. Therefore, we usually do not use EPDM as the default sealing material for quick coupling products. When customers need to use this type of sealing ring(EPDM), they need to send requirements to us. In our online store, it is usually not possible to buy quick couplings equipped with this type of sealing ring material(EPDM). If the quick connector you need needs to be installed in an application that passes through water or steam, EPDM will be a good replacement sealing material. It can extend the service life.
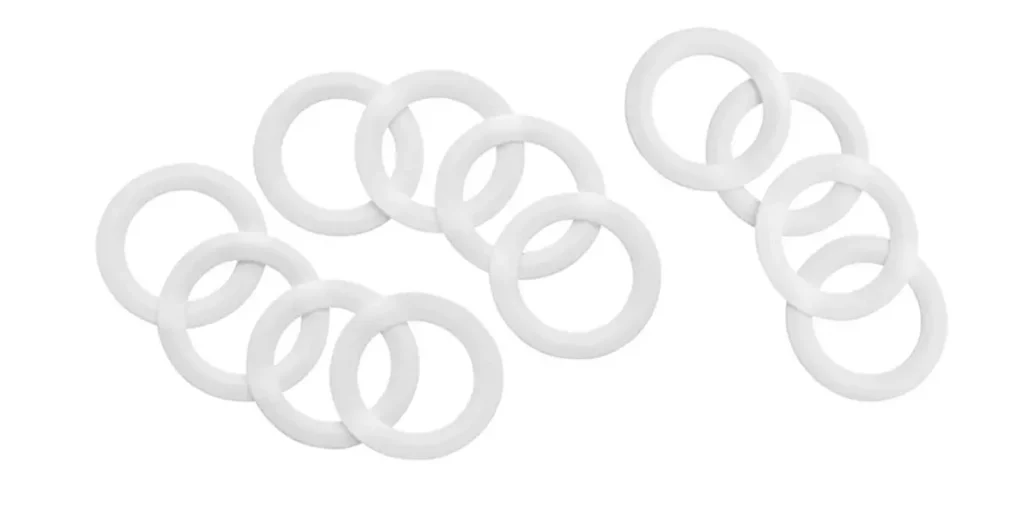
4. PTFE (Polytetrafluoroethylene)
Polytetrafluoroethylene (PTFE) is a high-performance synthetic fluoropolymer widely known for its remarkable chemical resistance, non-stick properties, and high-temperature tolerance. In quick couplings, PTFE is often used for gaskets. They are used together with seal rings which would be the material of NBR or FKM or EPDM. Here’s an in-depth look at PTFE:
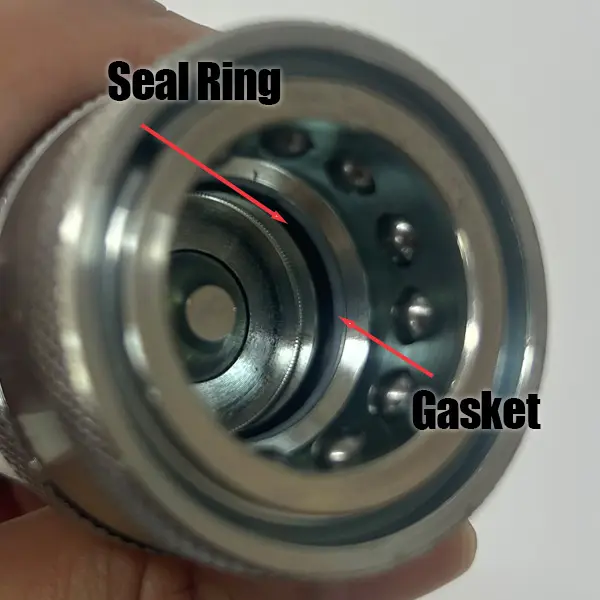
Properties of PTFE
- Chemical Resistance: PTFE is almost completely inert to a wide range of chemicals, including acids, bases, and solvents. This exceptional chemical resistance makes it ideal for use in aggressive chemical environments.
- Temperature Tolerance: PTFE can withstand temperatures ranging from -200°C to 260°C (-328°F to 500°F), making it suitable for both cryogenic and high-temperature applications.
- Non-Stick Properties: PTFE has a very low coefficient of friction, which gives it excellent non-stick properties. This is why PTFE is often used as a coating for cookware and other surfaces where sticking is undesirable.
- Electrical Insulation: PTFE is an excellent electrical insulator, maintaining its insulating properties across a wide range of temperatures and frequencies.
- Low Water Absorption: PTFE is highly hydrophobic, meaning it repels water and does not absorb moisture. This makes it suitable for applications where water resistance is critical.
- Mechanical Properties: PTFE has good mechanical strength, though it is softer than some other engineering plastics. It can be reinforced with fillers such as glass or carbon to enhance its mechanical properties.
Advantages of PTFE
- Inertness: Its chemical inertness makes PTFE suitable for use with almost any chemical substance.
- Temperature Range: PTFE’s ability to withstand both extremely low and high temperatures makes it versatile for many different environments.
- Low Friction: Its non-stick properties result in low friction, which can reduce wear and energy consumption in moving parts.
- Electrical Insulation: PTFE’s excellent insulating properties make it valuable in electrical and electronic applications.
- Hydrophobicity: Its resistance to water absorption adds to its durability in wet environments.
Limitations of PTFE
- Mechanical Strength: While PTFE has good mechanical properties, it is softer and more prone to deformation under load than some other engineering plastics.
- Wear and Creep: PTFE can exhibit wear and creep under mechanical stress, especially at elevated temperatures. Reinforcing with fillers can mitigate this to some extent.
- Cost: PTFE can be more expensive than other plastics, which might be a consideration in cost-sensitive applications.
PTFE is a versatile and highly valuable material known for its outstanding chemical resistance, temperature tolerance, and non-stick properties. Its unique characteristics make it indispensable in a wide range of industries, from chemical processing and electrical insulation to medical devices and food processing. In quick couplings, we usually use PTFE materials as gaskets. Then use them in conjunction with sealing rings made of other materials ( NBR, FKM etc.). The gasket is mainly used to ensure static sealing. That is, to ensure sealing in the connected state. And it can prevent the displacement of the sealing ring during the connection process of the quick connector.
5. Silicone Rubber
Silicone Rubber is a highly versatile and widely used synthetic elastomer known for its excellent temperature resistance, flexibility, and durability. It offers good resistance to many chemicals, including water, oxidizing agents, and some acids and alkalis. However, it is not suitable for use with most concentrated solvents, oils, and fuels. Therefore, silicone rubber is not usually used in quick connector products. However, in some special application scenarios, customers may require that the sealing ring material we usually use be replaced with this silicone rubber.
Biocompatibility
Silicone rubber is non-toxic and biocompatible, which allows it to be used in medical and food-related applications. This is one of the reasons why we receive some requests from customers to switch to silicone rubber. Because in the food industry, although EPDM can also come into contact with food, silicone rubber is obviously safer for food. Some beverage manufacturers will require customized quick connectors using silicone rubber seals.
Choosing the Right Material
Selecting the appropriate seal ring material involves considering several factors:
Chemical Compatibility
Ensure that the seal ring material is compatible with the fluids and chemicals it will be exposed to. This prevents degradation and extends the life of the coupling.
Temperature Range
Consider the operating temperature range of the application. The material should maintain its properties and performance within this range.
Environmental Factors
Evaluate the environmental conditions, such as exposure to UV light, ozone, and weathering. Choose a material that can withstand these factors without deteriorating.
Mechanical Properties
Assess the mechanical requirements, including flexibility, hardness, and compression set. The material should provide a reliable seal under varying pressures and movements.
Conclusion
Most hydraulic quick couplings use NBR as the seal ring material, and PTFE as the gasket. They are usually installed together in the groove inside the quick coupling. When the quick coupling is connected, the seal ring will provide most of the sealing work. Once connected, the gasket will provide more sealing work. FKM is often used as another option. Especially in stainless steel or brass quick couplings, the brass or stainless steel quick coupling may pass some different fluids (out of hydraulic oil). Or the operating temperature may be higher than 100˚C. Therefore, FKM is the default seal material to adapt to the use environment. EPDM is often installed as a seal material according to customer requirements.
Leave a Reply