Cuando se trata de acabado de metales, elegir el tipo de recubrimiento adecuado es crucial para la longevidad, la apariencia y el rendimiento de sus componentes. Entre las diversas opciones disponibles, el recubrimiento de zinc y el recubrimiento de zinc-níquel son dos opciones populares. La mayoría de los acoplamientos rápidos están hechos de acero al carbono porque es más rentable y puede soportar alta presión. El acero al carbono endurecido se utiliza a menudo para acoplamientos rápidos de alta presión en sistemas hidráulicos. Sin embargo, la resistencia a la corrosión es el mayor inconveniente. A menudo se requiere recubrimiento. El recubrimiento de zinc y el recubrimiento de zinc-níquel son los dos métodos de recubrimiento más comunes. Cada uno tiene ventajas distintivas y aplicaciones específicas en las que sobresalen. En este blog, profundizaremos en las diferencias entre el recubrimiento de zinc y el recubrimiento de zinc-níquel, exploraremos sus beneficios y lo ayudaremos a tomar una decisión informada para sus necesidades.
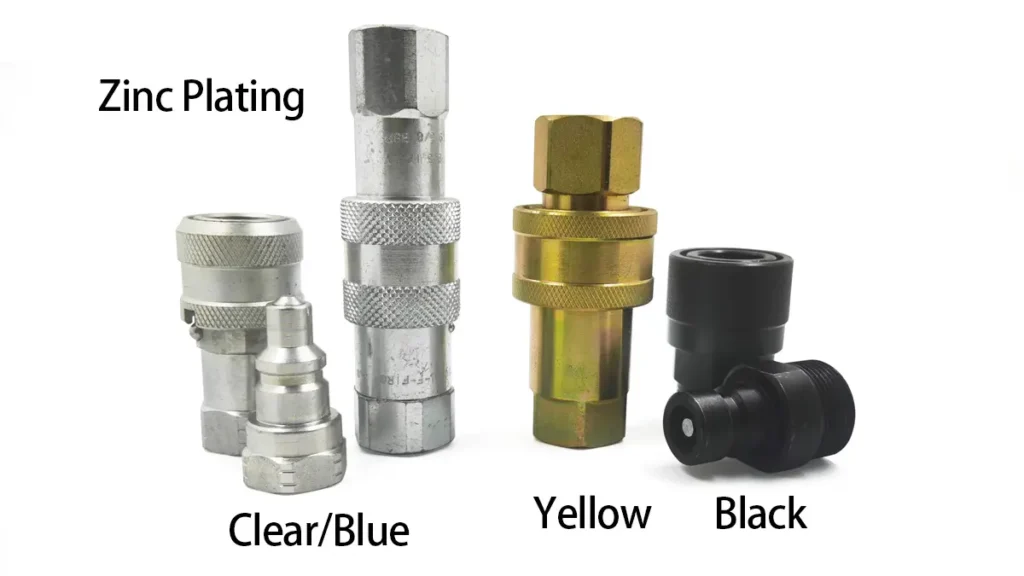
Entendiendo el enchapado de zinc
El galvanizado es un proceso muy popular para la protección de una amplia gama de componentes. Es un revestimiento de sacrificio que ofrece una excelente resistencia a la corrosión a un precio rentable. El galvanizado también se conoce como galvanización y se puede pasivar en varios colores.
Recubrimiento de zinc trivalente
El enchapado de zinc trivalente es un método de acabado que utiliza principalmente sulfato de cromo o cloruro de cromo, lo que lo hace respetuoso con el medio ambiente debido a la toxicidad reducida de estos ingredientes. Este tipo de enchapado, también conocido como cromado decorativo, comparte muchas características con el enchapado de zinc hexavalente, incluida la resistencia a los rayones y la corrosión. Además, ofrece una variedad de opciones de color.
Recubrimiento de zinc hexavalente
El enchapado de zinc hexavalente, comúnmente conocido como cromado, es un método de enchapado de zinc más antiguo que se utiliza tanto para acabados decorativos como funcionales. Este proceso implica sumergir el material del sustrato en un baño que contiene trióxido de cromo (CrO3) y ácido sulfúrico, lo que da como resultado un revestimiento que proporciona resistencia a la corrosión y al desgaste.
Sin embargo, debido a sus importantes desventajas, el galvanizado hexavalente ha sido reemplazado en gran medida por el galvanizado trivalente. El proceso genera productos de desecho peligrosos, como cromato de plomo y sulfato de bario. Además, el cromo hexavalente es un carcinógeno conocido, lo que hace que este método sea perjudicial tanto para la salud humana como para el medio ambiente. El 21 de septiembre de 2017, el cromo hexavalente estará sujeto a mayores restricciones después de haber estado incluido en la lista del Anexo de la Agencia Europea de Sustancias y Mezclas Químicas durante algún tiempo.
Diferencias entre el galvanizado trivalente y hexavalente
El galvanizado trivalente tiene varias ventajas:
- Puede crear depósitos altamente protectores y brillantes a densidades de corriente muy altas.
- Los depósitos presentan baja tensión y están libres de ampollas.
- Ofrece un excelente poder cubriente y uniformidad.
- Es respetuoso con el medio ambiente.
Sin embargo, existen algunos desafíos y desventajas asociados con el recubrimiento de zinc trivalente:
- El proceso es difícil de controlar.
- Los productos químicos utilizados son muy caros en comparación con el recubrimiento de zinc hexavalente.
- Los colores producidos no siempre son idénticos.
- El recubrimiento debe aplicarse a altas temperaturas, normalmente entre 30 y 60 °C.
Variación de color
El enchapado de zinc, ya sea trivalente o hexavalente, se puede producir en varios colores, lo que aumenta su versatilidad para aplicaciones decorativas y funcionales. Las opciones de color para el enchapado de zinc incluyen:
- Transparente/Azul: A menudo se utiliza para un acabado estándar, no decorativo, que proporciona resistencia básica a la corrosión.
- Amarillo: Proporciona un mayor nivel de resistencia a la corrosión y se utiliza a menudo para aplicaciones industriales.
- Negro: Se utiliza comúnmente con fines estéticos y proporciona buena resistencia a la corrosión.
- Verde oliva: se utiliza normalmente para aplicaciones militares debido a sus propiedades de camuflaje y no reflectantes.
Cada color se logra agregando diferentes productos químicos durante el proceso de enchapado, lo que permite la personalización según requisitos y preferencias específicos.
Ventajas del galvanizado
- Resistencia a la corrosión: el zinc actúa como una capa de sacrificio, corroyéndose antes que el metal subyacente, protegiendo así la pieza contra el óxido.
- Rentable: el recubrimiento de zinc es relativamente económico en comparación con otros tipos de recubrimiento de metal.
- Atractivo estético: proporciona un acabado brillante y suave que puede ser estéticamente agradable y puede mejorarse aún más con varios tratamientos de cromado.
- Facilidad de aplicación: El proceso es sencillo y se puede aplicar a una variedad de formas y tamaños.
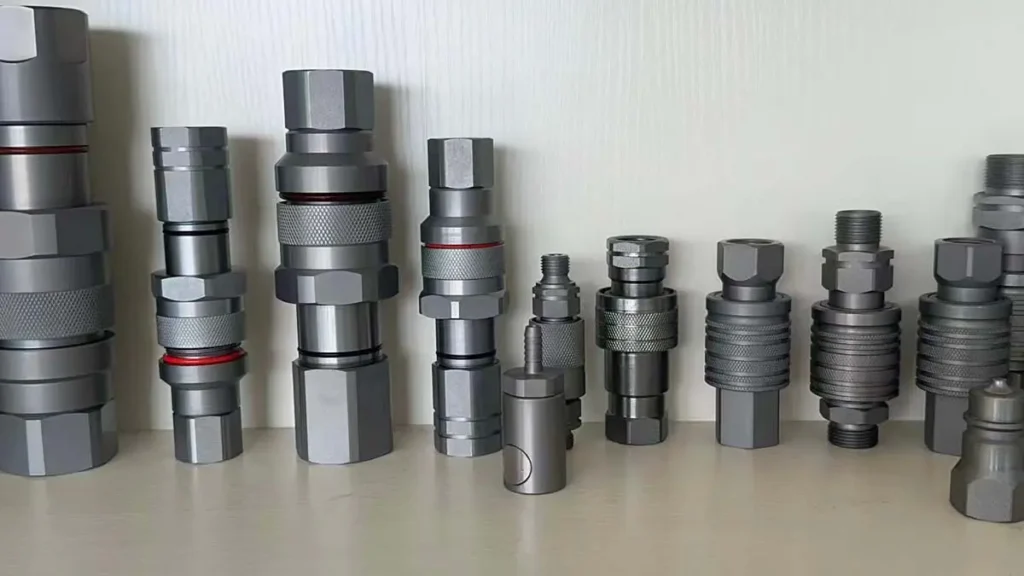
Entendiendo el enchapado de zinc y níquel
Por otro lado, el enchapado de zinc-níquel implica un proceso más complejo en el que se aplica una capa de aleación de zinc-níquel al sustrato. Normalmente, la aleación consta de un 85-92 % de zinc y un 8-15 % de níquel. Esta combinación da como resultado un recubrimiento que ofrece un rendimiento superior en varias áreas en comparación con el enchapado de zinc estándar.
El enchapado de zinc-níquel es una técnica de galvanoplastia avanzada que combina zinc y níquel para crear un revestimiento protector superior sobre diversos sustratos, principalmente acero y hierro. Este método ha ganado popularidad debido a su excelente resistencia a la corrosión, durabilidad y versatilidad, lo que lo convierte en una opción preferida en muchas industrias, incluidas la automotriz, la aeroespacial y la electrónica.
Ventajas del recubrimiento de zinc-níquel
- Resistencia superior a la corrosión: los recubrimientos de zinc-níquel brindan una excelente protección contra la corrosión, superando significativamente el recubrimiento de zinc tradicional. Esto los hace ideales para piezas expuestas a entornos hostiles, como componentes automotrices sujetos a sales de carretera y equipos marinos. Los acoplamientos rápidos se utilizan en maquinaria de ingeniería en entornos hostiles y, por lo general, requieren un recubrimiento de zinc-níquel.
- Alta durabilidad: la aleación de zinc-níquel ofrece una mayor resistencia al desgaste, lo que la hace adecuada para aplicaciones en las que los componentes están sujetos a estrés mecánico y fricción. Por lo tanto, en algunos sistemas hidráulicos de alta intensidad, los acoplamientos rápidos también deben utilizar un revestimiento de zinc-níquel, como algunos acoplamientos rápidos de cara plana con tornillos en aplicaciones de martillos hidráulicos.
- Resistencia al calor: Los recubrimientos de zinc-níquel pueden soportar temperaturas más altas en comparación con los recubrimientos de zinc puro, lo que los hace adecuados para aplicaciones en entornos de alta temperatura, como piezas de acoplamiento rápido debajo del capó.
- Recubrimiento uniforme: El proceso de recubrimiento garantiza un recubrimiento consistente y uniforme, proporcionando una protección integral incluso en geometrías complejas y piezas intrincadas.
- Respetuoso con el medio ambiente: el enchapado de cinc-níquel es una alternativa respetuosa con el medio ambiente al enchapado de cromo hexavalente, conocido por sus propiedades tóxicas y cancerígenas. Esto hace que el enchapado de cinc-níquel sea una opción más segura tanto para los trabajadores como para el medio ambiente.
Aplicaciones del recubrimiento de zinc-níquel
Además de utilizarse en algunos de nuestros productos de acoplamiento rápido de alta demanda, el enchapado de zinc-níquel también se utiliza en las siguientes industrias. Puede ayudarle a comprender el rendimiento del enchapado de zinc-níquel.
- Industria automotriz: ampliamente utilizado para componentes debajo del capó, sujetadores, pinzas de freno y piezas del sistema de combustible, el revestimiento de zinc-níquel proporciona la durabilidad y la resistencia a la corrosión necesarias para soportar las condiciones desafiantes de las aplicaciones automotrices.
- Industria aeroespacial: En la industria aeroespacial, el recubrimiento de zinc-níquel se aplica a componentes que requieren alta resistencia, resistencia al desgaste y capacidad para soportar temperaturas extremas, como el tren de aterrizaje y las piezas del motor.
- Electrónica: Los recubrimientos de zinc-níquel se utilizan en conectores y componentes electrónicos para garantizar la longevidad y la confiabilidad, especialmente en entornos propensos a la corrosión.
- Equipos industriales: Diversos equipos y maquinarias industriales se benefician del recubrimiento de zinc-níquel, que mejora su vida útil y rendimiento al protegerlos contra el desgaste y la corrosión.
El enchapado de zinc-níquel se destaca como una solución de tratamiento de superficies robusta y versátil, que ofrece una resistencia superior a la corrosión, durabilidad y beneficios ambientales. Su amplia gama de aplicaciones en múltiples industrias subraya su importancia y eficacia para mejorar el rendimiento y la longevidad de los componentes metálicos. A medida que las industrias continúan buscando soluciones de recubrimiento avanzadas y sostenibles, el enchapado de zinc-níquel sigue a la vanguardia, estableciendo un alto estándar para los acabados protectores de metales.
Comparación del rendimiento del enchapado de zinc y del enchapado de zinc-níquel
Al evaluar el rendimiento del enchapado de zinc frente al enchapado de zinc-níquel, varios factores clave destacan las características superiores del enchapado de zinc-níquel. Estos factores incluyen la resistencia a la corrosión, la resistencia al desgaste y la estabilidad ambiental, que son cruciales para diversas aplicaciones industriales.
Resistencia a la corrosión
Rendimiento de la prueba de niebla salina
- Recubrimiento de zinc: el recubrimiento de zinc generalmente ofrece una resistencia moderada a la corrosión. En las pruebas estándar de niebla salina (ASTM B117), los componentes recubiertos de zinc generalmente resisten entre 100 y 500 horas antes de que aparezca óxido rojo, según el espesor del revestimiento y la presencia de capas de pasivación. En el caso de los productos de acoplamiento rápido convencionales con recubrimiento de zinc, generalmente los probamos durante 100 horas en la prueba de niebla salina para garantizar que se puedan usar en entornos operativos normales.
- Recubrimiento de zinc-níquel: el recubrimiento de zinc-níquel se destaca por su resistencia a la corrosión, y suele resistir entre 1000 y 2000 horas en pruebas de niebla salina antes de que aparezca óxido rojo. Este rendimiento significativamente superior hace que el recubrimiento de zinc-níquel sea ideal para entornos con alta humedad, salinidad y exposición a sustancias corrosivas. Por lo general, realizamos más de 500 horas de pruebas de niebla salina para garantizar que el producto se pueda utilizar en un entorno más severo. Solo si el cliente tiene requisitos más específicos, realizaremos entre 1000 y 2000 horas de pruebas de niebla salina.
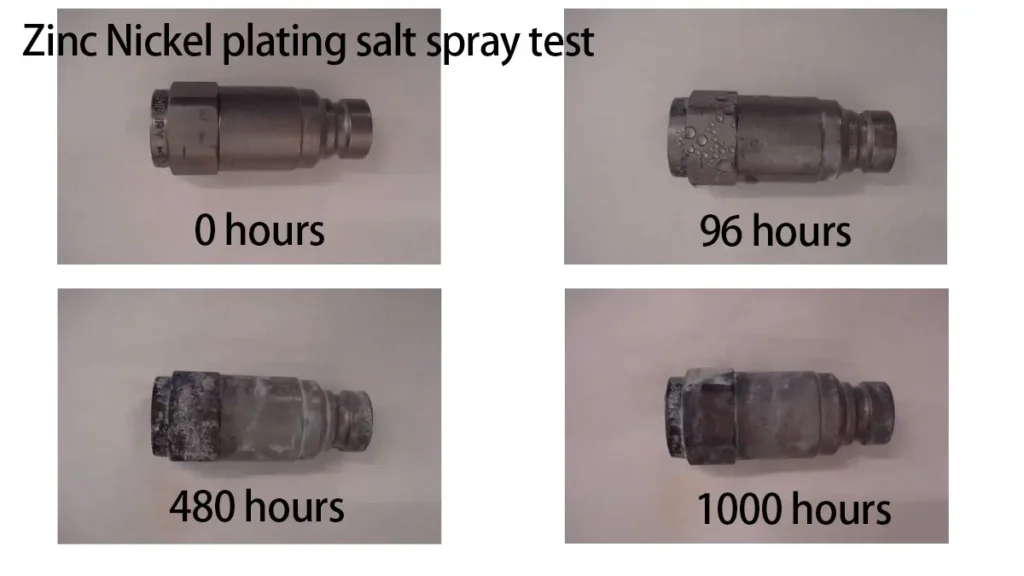
Resistencia al desgaste
- Recubrimiento de zinc: si bien el recubrimiento de zinc proporciona cierto nivel de resistencia al desgaste, se valora principalmente por su protección contra la corrosión. Su resistencia al desgaste es generalmente menor, lo que lo hace menos adecuado para aplicaciones que impliquen un estrés mecánico o fricción significativos. Los acoplamientos rápidos utilizan el proceso de galvanizado. Durante el transporte o el uso, pueden aparecer algunos rayones causados por colisiones en la superficie, lo cual es un fenómeno muy normal.
- Recubrimiento de zinc-níquel: la inclusión de níquel en la aleación mejora significativamente la resistencia al desgaste. Los recubrimientos de zinc-níquel son más duros y duraderos, lo que los hace más adecuados para piezas sujetas a desgaste mecánico. Los acoplamientos rápidos con recubrimiento de zinc-níquel no dejarán rayones en la superficie y no habrá desgaste evidente en la conexión del acoplamiento rápido, lo que puede extender efectivamente la vida útil del acoplamiento rápido. Si el usuario puede reemplazar el anillo de sellado, el costo de reemplazo puede reducirse en gran medida.
Resistencia al calor
- Recubrimiento de zinc: el recubrimiento de zinc puede tolerar temperaturas moderadas, pero puede degradarse o perder cualidades protectoras a temperaturas más altas, generalmente superiores a 120 °C (248 °F).
- Recubrimiento de zinc-níquel: Los recubrimientos de zinc-níquel mantienen su integridad a temperaturas más altas, a menudo hasta 300 °C (572 °F), lo que los hace adecuados para aplicaciones de alta temperatura, como componentes debajo del capó de automóviles y piezas aeroespaciales.
Los acoplamientos rápidos rara vez se utilizan a temperaturas tan altas, porque lo primero que no soporta las altas temperaturas es el material de sellado. Sin embargo, en algunos entornos, como cerca del motor o donde el fluido interno alcanza una temperatura de más de 100 °C, además de considerar la elección de los materiales de sellado, también tenemos en cuenta la cuestión del recubrimiento. Pero en ocasiones lo sustituiremos por acero inoxidable, que no requiere recubrimiento.
Adherencia y uniformidad
- Recubrimiento de zinc: proporciona un recubrimiento uniforme y suave que se adhiere bien a diversos sustratos, pero el espesor puede variar en geometrías complejas, lo que puede generar una protección desigual.
- Recubrimiento de zinc-níquel: ofrece una excelente adherencia y uniformidad incluso en piezas complejas. El proceso garantiza una capa uniforme que brinda protección integral en toda la superficie.
En proyectos de acoplamientos rápidos personalizados, si los requisitos de diseño del producto son más complejos, generalmente recomendamos el uso de revestimiento de zinc-níquel. Debido a que el revestimiento de zinc-níquel es más uniforme para productos complejos y tiene una adhesión mucho mejor que la galvanización. Algunos clientes de la industria del gas natural comprimido en los Estados Unidos finalmente eligieron acoplamientos rápidos de acero al carbono con revestimiento de zinc-níquel después de usar acoplamientos rápidos de acero inoxidable y acoplamientos rápidos de acero al carbono con revestimiento de zinc-níquel. Además de las consideraciones de costo, el rendimiento del revestimiento de zinc-níquel no es peor que el del acero inoxidable, y también es muy resistente al desgaste y tiene una larga vida útil.
Impacto ambiental
- Galvanizado: el galvanizado tradicional, especialmente cuando se utiliza cromo hexavalente para la pasivación, plantea riesgos ambientales y para la salud debido a la toxicidad de los compuestos de cromo hexavalente. Casi hemos abandonado el proceso de galvanizado con cromo hexavalente y ahora utilizamos el proceso de galvanizado con cromo trivalente.
- Recubrimiento de zinc-níquel: El recubrimiento de zinc-níquel es más respetuoso con el medio ambiente, especialmente cuando se utiliza pasivación con cromo trivalente, que es menos tóxico y más seguro tanto para los trabajadores como para el medio ambiente.
Costo
- Recubrimiento de zinc: generalmente menos costoso que el recubrimiento de zinc-níquel, lo que lo convierte en una solución rentable para aplicaciones con requisitos de rendimiento moderados.
- Recubrimiento de zinc-níquel: mayor costo inicial debido al proceso de recubrimiento más complejo y al costo del níquel, pero ofrece un rendimiento superior que puede reducir los costos de mantenimiento y reemplazo a lo largo del tiempo.
En términos generales, para el mismo producto de acoplamiento rápido, el que utiliza el proceso de galvanizado es aproximadamente un 10% más barato que el que utiliza el proceso de niquelado de zinc. Sin embargo, la durabilidad del producto aumentará entre un 25% y un 30%. Debido a que la superficie es más resistente al desgaste, si el cliente reemplaza el anillo de sellado, se puede aumentar el tiempo de uso.
Conclusión
Si bien tanto el enchapado de zinc como el enchapado de zinc-níquel proporcionan valiosos recubrimientos protectores, el enchapado de zinc-níquel se destaca por su resistencia superior a la corrosión, resistencia al desgaste y estabilidad ambiental. Estas ventajas lo convierten en la opción preferida para aplicaciones exigentes donde la longevidad y la confiabilidad son fundamentales. Si bien tiene un costo inicial más alto, el rendimiento y la durabilidad mejorados del enchapado de zinc-níquel a menudo justifican la inversión en acoplamientos rápidos de alto rendimiento.