When it comes to metal finishing, choosing the right type of plating is crucial for the longevity, appearance, and performance of your components. Among the various options available, zinc plating and zinc-nickel plating are two popular choices. Most quick couplings are made of carbon steel because it is more cost-effective and can withstand high pressure. Hardened Carbon steel is often used for high-pressure quick couplings in hydraulic systems. However, corrosion resistance is the biggest drawback. Plating is often required. zinc plating and zinc-nickel plating are the two most common plating methods. Each has distinct advantages and specific applications where they excel. In this blog, we’ll delve into the differences between zinc plating and zinc-nickel plating, exploring their benefits, and helping you make an informed decision for your needs.
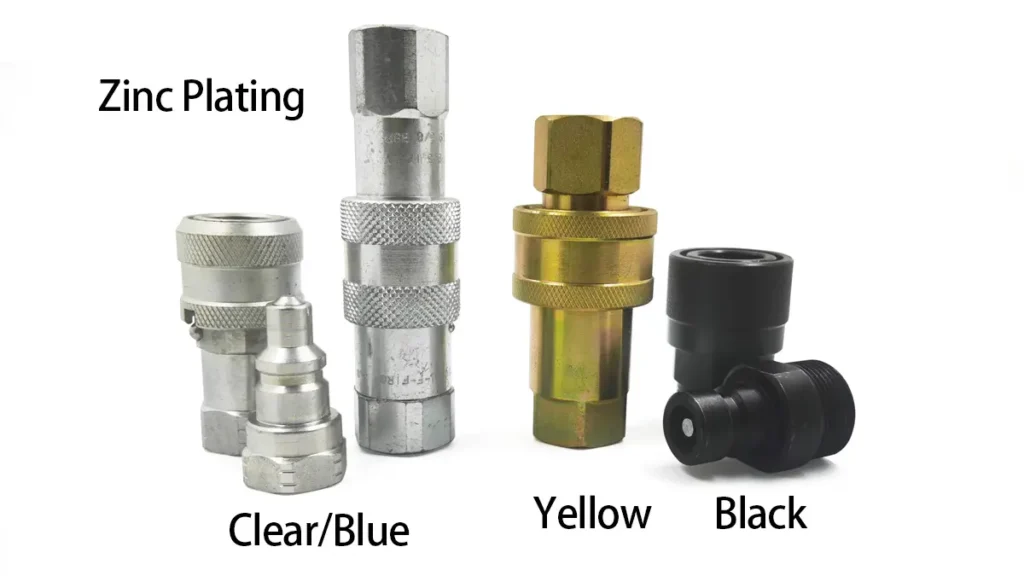
Understanding Zinc Plating
Zinc Plating is a very popular process for the protection of a wide range of components. It’s a sacrificial coating that offers excellent corrosion resistance at a cost effective price. Zinc Plating is also known as galvanising and can be passivated in a number of colours.
Trivalent Zinc Plating
Trivalent zinc plating is a finishing method that primarily uses chromium sulfate or chromium chloride, making it environmentally friendly due to the reduced toxicity of these ingredients. This type of plating, also known as decorative chrome plating, shares many characteristics with hexavalent zinc plating, including scratch and corrosion resistance. Additionally, it offers a variety of color options.
Hexavalent Zinc Plating
Hexavalent zinc plating, commonly known as chrome plating, is an older zinc plating method used for both decorative and functional finishes. This process involves submerging the substrate material in a bath containing chromium trioxide (CrO3) and sulfuric acid, resulting in a coating that provides corrosion and wear resistance.
However, due to its significant disadvantages, hexavalent zinc plating has been largely replaced by trivalent zinc plating. The process generates hazardous waste products, such as lead chromate and barium sulfate. Additionally, hexavalent chromium is a known carcinogen, making this method harmful to both human health and the environment. On the 21st September 2017, Hexavalent Chrome will be subject to increased restrictions after being placed on the European Chemicals Agency’s Annex list for some time.
Differences Between Trivalent and Hexavalent Zinc Plating
Trivalent zinc plating has several advantages:
- It can create highly protective and bright deposits at very high current densities.
- The deposits are low-stress and free of blisters.
- It offers excellent covering power and uniformity.
- It is environmentally friendly.
However, there are some challenges and disadvantages associated with trivalent zinc plating:
- The process is difficult to control.
- The chemicals used are highly expensive comparing with Hexavalent Zinc plating
- The colors produced are not always identical.
- The coating must be applied at high temperatures, typically between 30-60°C.
Color Variation
Zinc plating, whether trivalent or hexavalent, can be produced in various colors, adding to its versatility for decorative and functional applications. The color options for zinc plating include:
- Clear/Blue: Often used for a standard, non-decorative finish that provides basic corrosion resistance.
- Yellow: Provides a higher level of corrosion resistance and is often used for industrial applications.
- Black: Commonly used for aesthetic purposes and provides good corrosion resistance.
- Olive Drab: Typically used for military applications due to its non-reflective, camouflaging properties.
Each color is achieved by adding different chemicals during the plating process, allowing for customization based on specific requirements and preferences.
Advantages of Zinc Plating
- Corrosion Resistance: Zinc acts as a sacrificial coating, corroding before the underlying metal does, thus protecting the part from rust.
- Cost-Effective: Zinc plating is relatively inexpensive compared to other types of metal plating.
- Aesthetic Appeal: Provides a shiny, smooth finish which can be aesthetically pleasing and can be further enhanced with various chromate treatments.
- Ease of Application: The process is straightforward and can be applied to a variety of shapes and sizes.
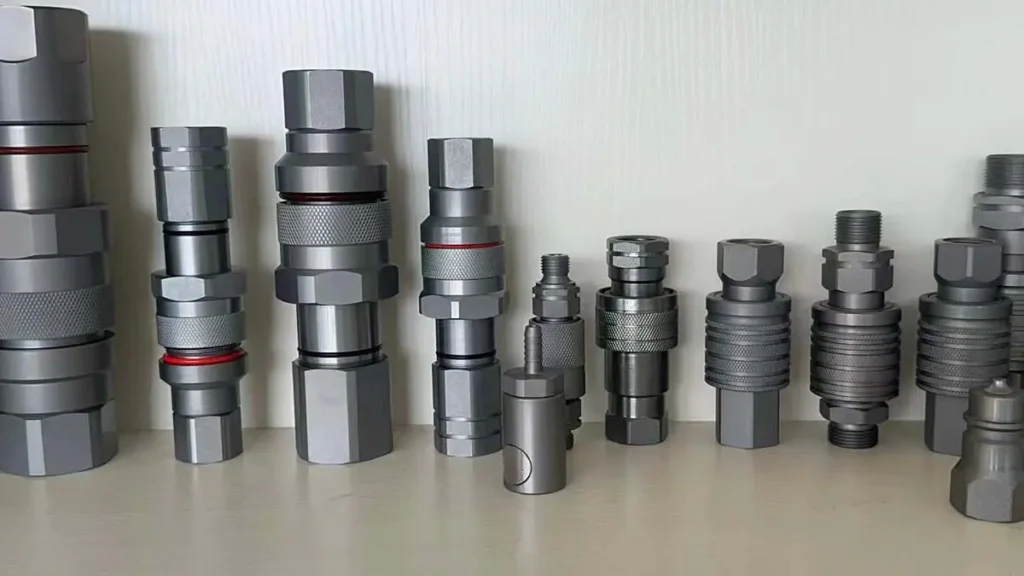
Understanding Zinc-Nickel Plating
Zinc-nickel plating, on the other hand, involves a more complex process where a layer of zinc-nickel alloy is applied to the substrate. Typically, the alloy consists of 85-92% zinc and 8-15% nickel. This combination results in a coating that offers superior performance in several areas compared to standard zinc plating.
Zinc-nickel plating is an advanced electroplating technique that combines zinc and nickel to create a superior protective coating on various substrates, primarily steel and iron. This method has gained popularity due to its excellent corrosion resistance, durability, and versatility, making it a preferred choice across many industries, including automotive, aerospace, and electronics.
Advantages of Zinc-Nickel Plating
- Superior Corrosion Resistance: Zinc-nickel coatings provide outstanding protection against corrosion, significantly outperforming traditional zinc plating. This makes it ideal for parts exposed to harsh environments, such as automotive components subject to road salts and marine equipment. Quick couplings are used in engineering machinery in harsh environments and usually require zinc-nickel plating.
- High Durability: The zinc-nickel alloy offers enhanced wear resistance, making it suitable for applications where components are subjected to mechanical stress and friction. Therefore, in some high-intensity hydraulic systems, quick couplings also need to use zinc-nickel plating, such as some screw flat face quick couplings in hydraulic hammer applications.
- Heat Resistance: Zinc-nickel coatings can withstand higher temperatures compared to pure zinc coatings, making them suitable for applications in high-temperature environments, such as under-the-hood quick coupling parts.
- Uniform Coating: The plating process ensures a consistent and uniform coating, providing comprehensive protection even on complex geometries and intricate parts.
- Environmentally Friendly: Zinc-nickel plating is an environmentally friendly alternative to hexavalent chromium plating, which is known for its toxic and carcinogenic properties. This makes zinc-nickel plating a safer option for both workers and the environment.
Applications of Zinc-Nickel Plating
In addition to being used on some of our high-demand quick coupling products, zinc-nickel plating is also used in the following industries. It can help you understand the performance of zinc-nickel plating.
- Automotive Industry: Widely used for under-the-hood components, fasteners, brake calipers, and fuel system parts, zinc-nickel plating provides the necessary durability and corrosion resistance to withstand the challenging conditions of automotive applications.
- Aerospace Industry: In aerospace, zinc-nickel plating is applied to components that require high strength, wear resistance, and the ability to endure extreme temperatures, such as landing gear and engine parts.
- Electronics: Zinc-nickel coatings are used in electronic connectors and components to ensure longevity and reliability, especially in environments prone to corrosion.
- Industrial Equipment: Various industrial machinery and equipment benefit from zinc-nickel plating, which enhances their lifespan and performance by protecting against wear and corrosion.
Zinc-nickel plating stands out as a robust and versatile surface treatment solution, offering superior corrosion resistance, durability, and environmental benefits. Its wide range of applications across multiple industries underscores its importance and effectiveness in enhancing the performance and longevity of metal components. As industries continue to seek advanced and sustainable coating solutions, zinc-nickel plating remains at the forefront, setting a high standard for protective metal finishes.
Comparing the Performance of Zinc Plating and Zinc-Nickel Plating
When evaluating the performance of zinc plating versus zinc-nickel plating, several key factors highlight the superior characteristics of zinc-nickel plating. These factors include corrosion resistance, wear resistance, and environmental stability, which are crucial for various industrial applications.
Corrosion Resistance
Salt Spray Test Performance
- Zinc Plating: Zinc plating typically offers moderate corrosion resistance. In standard salt spray tests (ASTM B117), zinc-plated components generally withstand 100-500 hours before red rust appears, depending on the thickness of the coating and the presence of passivation layers. For conventional quick coupling products with Zinc plalting, we usually test them for 100 hours in salt spray test to ensure they can be used in normal operating environments.
- Zinc-Nickel Plating: Zinc-nickel plating excels in corrosion resistance, often enduring 1000-2000 hours in salt spray tests before red rust appears. This significantly higher performance makes zinc-nickel plating ideal for environments with high humidity, salinity, and exposure to corrosive substances. We usually do more than 500 hours of salt spray test to ensure that the product can be used in a more severe environment. Only if the customer has more specific requirements, we will do 1000-2000 hours of salt spray test.
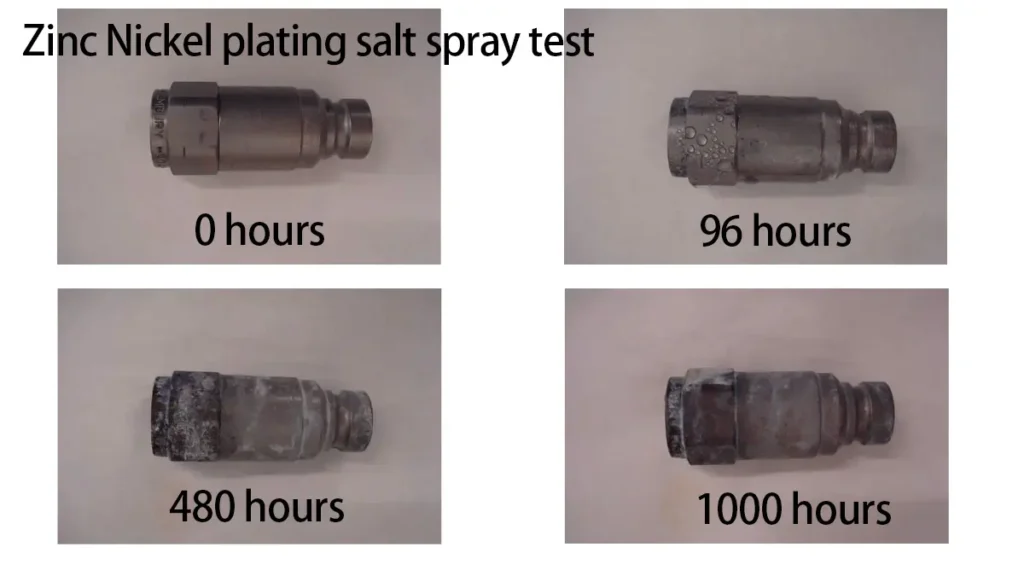
Wear Resistance
- Zinc Plating: While zinc plating provides some level of wear resistance, it is primarily valued for its sacrificial protection against corrosion. Its wear resistance is generally lower, making it less suitable for applications involving significant mechanical stress or friction. The quick couplings use the galvanizing process. During transportation or use, some scratches caused by collisions may appear on the surface, which is a very normal phenomenon.
- Zinc-Nickel Plating: The inclusion of nickel in the alloy significantly enhances wear resistance. Zinc-nickel coatings are harder and more durable, making them better suited for parts subjected to mechanical wear and tear. The quick couplings with zinc-nickel plating will not leave scratches on the surface, and there will be no obvious wear and tear at the quick coupling connection, which can effectively extend the service life of the quick coupling. If the user can replace the sealing ring, the replacement cost can be greatly reduced.
Heat Resistance
- Zinc Plating: Zinc plating can tolerate moderate temperatures but may degrade or lose protective qualities at higher temperatures, typically above 120°C (248°F).
- Zinc-Nickel Plating: Zinc-nickel coatings maintain their integrity at higher temperatures, often up to 300°C (572°F), making them suitable for high-temperature applications such as automotive under-hood components and aerospace parts.
Quick couplings are rarely used at such high temperatures, because the first thing that cannot withstand high temperatures is the sealing material. However, in some environments, such as near the engine or where the internal fluid reaches a temperature of more than 100°C, in addition to considering the choice of sealing materials, we also consider the issue of coating. But sometimes we will replace it with stainless steel, which does not require coating.
Adhesion and Uniformity
- Zinc Plating: Provides a uniform and smooth coating that adheres well to various substrates, but the thickness can vary on complex geometries, potentially leading to uneven protection.
- Zinc-Nickel Plating: Offers excellent adhesion and uniformity even on intricate parts. The process ensures a consistent layer that provides comprehensive protection across the entire surface.
In custom quick coupling projects, if the product design requirements are more complex, we usually recommend the use of zinc-nickel plating. Because zinc-nickel plating is more uniform for complex products and has much better adhesion than galvanizing. Some customers in the compressed natural gas industry in the United States finally chose zinc-nickel-plated carbon steel quick couplings after using stainless steel quick couplings and zinc-nickel-plated carbon steel quick couplings. In addition to cost considerations, the performance of zinc-nickel plating is not worse than stainless steel, and it is also very wear-resistant and has a long service life.
Environmental Impact
- Zinc Plating: Traditional zinc plating, especially when using hexavalent chromium for passivation, poses environmental and health risks due to the toxicity of hexavalent chromium compounds. We have almost abandoned the hexavalent chromium galvanizing process and are now using the trivalent chromium galvanizing process.
- Zinc-Nickel Plating: Zinc-nickel plating is more environmentally friendly, particularly when using trivalent chromium passivation, which is less toxic and safer for both workers and the environment.
Cost
- Zinc Plating: Generally less expensive than zinc-nickel plating, making it a cost-effective solution for applications with moderate performance requirements.
- Zinc-Nickel Plating: Higher initial cost due to the more complex plating process and the cost of nickel, but offers superior performance that can reduce maintenance and replacement costs over time.
Generally speaking, for the same quick coupling product, the one using galvanizing process is about 10% cheaper than the one using zinc-nickel plating. However, the product durability will be increased by 25%-30%. Because the surface is more wear-resistant, if the customer replaces the seal ring, the usage time can be increased.
Conclusion
While both zinc plating and zinc-nickel plating provide valuable protective coatings, zinc-nickel plating stands out for its superior corrosion resistance, wear resistance, and environmental stability. These advantages make it the preferred choice for demanding applications where longevity and reliability are critical. Although it comes at a higher initial cost, the enhanced performance and durability of zinc-nickel plating often justify the investment in high-performance quick couplings.
Leave a Reply