Hydraulic systems are the lifeblood of many industrial and mobile machinery applications, and the quick couplings used in these systems are critical components. These couplings allow for the swift and efficient connection and disconnection of hydraulic lines without fluid leakage or system contamination. One of the key factors that influence the performance and longevity of hydraulic quick couplings is the material they are made from. In this guide, we’ll explore the various materials used in hydraulic quick couplings, including carbon steel with zinc or zinc-nickel plating, brass, stainless steel, and aluminum, to help you choose the best option for your specific needs.
1.Carbon Steel with Zinc Plating or Zinc-Nickel Plating
Carbon steel is a popular choice for hydraulic quick couplings due to its strength and durability. However, carbon steel is susceptible to corrosion, which can compromise the integrity of the coupling over time. To combat this, carbon steel couplings are often coated with zinc or zinc-nickel plating.
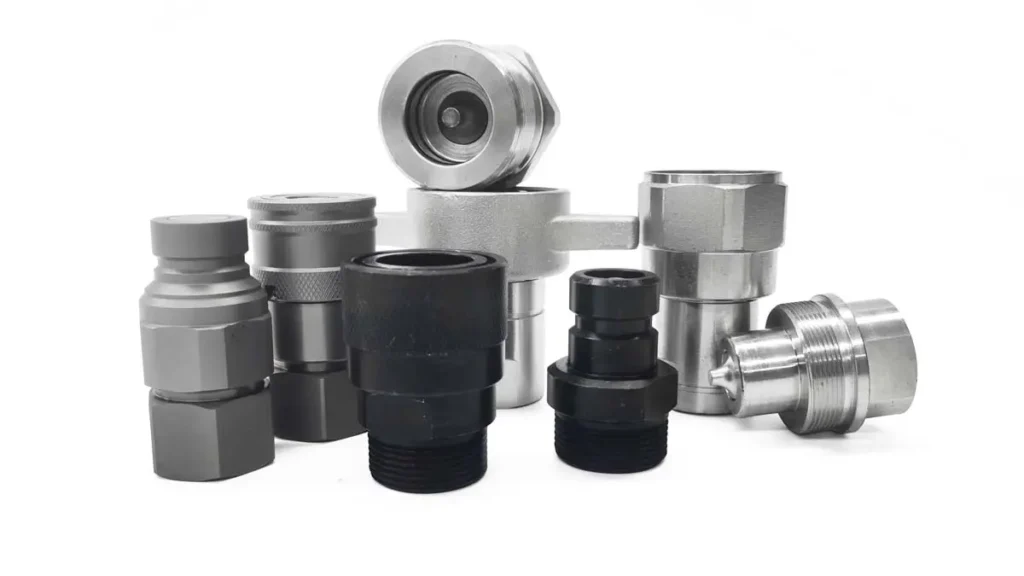
Zinc Plating
- Corrosion Resistance: Zinc plating provides a basic level of corrosion protection by acting as a sacrificial layer. It corrodes first, thereby protecting the underlying steel.
- Cost-Effective: This plating is relatively inexpensive, making it an economical choice for many applications.
- Applications: Suitable for indoor or controlled environments where exposure to corrosive elements is minimal.
Zinc-Nickel Plating
- Enhanced Protection: Zinc-nickel plating offers superior corrosion resistance compared to standard zinc plating. The addition of nickel significantly improves the durability of the coating.
- Longer Lifespan: This type of plating is particularly beneficial in harsh environments, such as those with high humidity or salt exposure.
- Applications: Ideal for outdoor or industrial environments where enhanced corrosion resistance is necessary.
Why Use Carbon Steel for Hydraulic Quick Couplings?
Carbon steel is a common material choice for hydraulic quick couplings due to its combination of strength, durability, and cost-effectiveness. Here are several reasons why carbon steel is used for these critical components:
High Strength and Durability
Carbon steel is known for its high tensile strength and durability, making it capable of withstanding the high pressures and mechanical stresses typical in hydraulic systems. This strength ensures that carbon steel quick couplings can endure demanding conditions without deforming or failing, which is crucial for maintaining the integrity and safety of hydraulic systems.
Cost-Effectiveness
Compared to other materials like stainless steel or specialized alloys, carbon steel is relatively inexpensive. This makes it a cost-effective choice for manufacturing hydraulic quick couplings, especially in large quantities. The affordability of carbon steel allows for the production of durable and reliable couplings without significantly driving up costs, which is beneficial for both manufacturers and end-users.
Good Machinability
Carbon steel is relatively easy to machine and fabricate into complex shapes, which is essential for producing precise hydraulic quick couplings. The good machinability of carbon steel allows for efficient manufacturing processes, resulting in high-quality couplings with accurate dimensions and consistent performance.
Surface Treatment for Enhanced Properties
While carbon steel itself is prone to corrosion, it can be treated with various coatings to enhance its resistance to environmental factors. Common treatments include:
- Zinc Plating: This provides a protective layer that resists rust and corrosion, extending the lifespan of the coupling. Zinc plating is relatively inexpensive and suitable for applications where moderate corrosion resistance is sufficient.
- Zinc-Nickel Plating: This offers superior corrosion resistance compared to standard zinc plating. The addition of nickel enhances the protective properties, making it suitable for harsher environments.
- Other Coatings: Various other coatings can be applied to improve wear resistance, reduce friction, and enhance overall durability.
Versatility in Applications
Carbon steel quick couplings are versatile and can be used in a wide range of applications, including:
- Industrial Machinery: Where high strength and durability are required to handle heavy loads and high pressures.
- Agricultural Equipment: For reliable performance in tough, outdoor environments.
- Construction Equipment: To withstand the rigorous demands and harsh conditions of construction sites.
- Automotive Industry: For hydraulic systems in vehicles that require strong and durable connections.
Impact and Wear Resistance
Carbon steel offers good resistance to impact and wear, which is important for hydraulic quick couplings subjected to repetitive connections and disconnections. This resistance helps prevent damage and extends the service life of the couplings, ensuring consistent performance over time.
Customizability
The properties of carbon steel can be adjusted through various heat treatment processes to meet specific requirements. For instance, through hardening and tempering, carbon steel can achieve the desired balance of hardness and toughness, making it suitable for different hydraulic applications.
Choosing carbon steel for hydraulic quick couplings offers several advantages, including high strength, durability, cost-effectiveness, and versatility. While carbon steel is inherently prone to corrosion, surface treatments like zinc or zinc-nickel plating significantly enhance its resistance to environmental factors, making it a practical choice for a wide range of applications. By understanding the benefits and applications of carbon steel, you can make an informed decision when selecting quick couplings for your hydraulic systems, ensuring reliable performance and longevity.
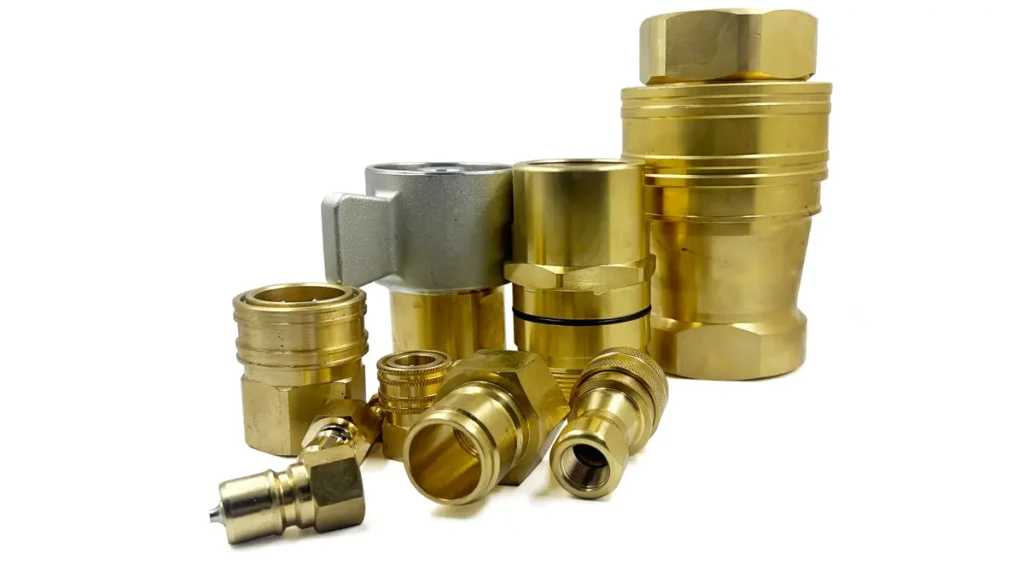
2.Brass
Brass is an alloy of copper and zinc, known for its excellent machinability and corrosion resistance. Unlike carbon steel, which requires protective coatings to prevent rust, brass resists corrosion on its own. Brass is compatible with a wide variety of hydraulic fluids, including water-based and oil-based fluids. This compatibility reduces the risk of chemical reactions that could degrade the coupling or contaminate the fluid. Brass is known for its excellent machinability, meaning it can be easily shaped and fabricated into precise components. Brass is generally more cost-effective than some other high-performance materials like stainless steel. It offers a good balance of performance, durability, and cost, making it a practical choice for many applications.
Applications of Brass Quick Couplings
Unlike carbon steel quick couplings, brass has a lower strength and is therefore not often used directly in hydraulic systems. Instead, it is widely used in applications that transport water or chemical liquids. It is also used in steam applications because of its excellent temperature resistance.
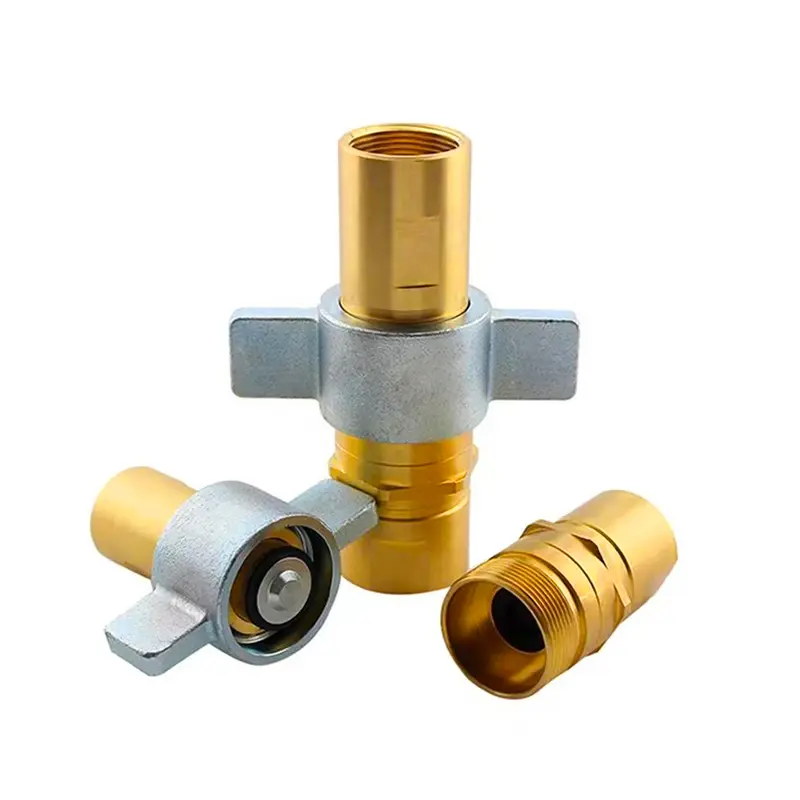
Wet-Line Kits
WSC Series are the quick couplings widely used in wet-line kits. the body material is brass and the wing nut is made from carbon steel. With their durable brass and steel construction, wing style design, and easy operation, these couplers ensure secure and leak-free connections in even the most demanding environments. Whether used in trailers, wet line kits, the oil and gas industry, construction equipment, industrial machinery, agricultural equipment, or mining, the WSC Series delivers unmatched performance and reliability, enhancing overall system productivity and safety.
Pressure Washer quick couplings
PWB Series – Brass Valveless Pressure Washer Couplers. High-Quality Brass Construction: Provides excellent durability and corrosion resistance, extending the lifespan of the couplers.
Carpet Extractors, steam applications
The 1/4″ or 3/8″ size ISO B Brass Quick Couplings are usually widely used in cleaning industries, especially for the carpet extractors. Usually used in steam sterilization connections. Very popular in the housekeeping industry in Europe and the United States. In the United States and Australia, this type of quick connector can be seen on the websites of many cleaning companies.
Natural gas quick connector
In household natural gas use, quick connectors are also widely used. In Canada and the United States, people use brass quick connectors because natural gas usually contains some moisture, but brass will not rust in long-term use.
Why Use Brass for Hydraulic Quick Couplings
Excellent Corrosion Resistance
One of the standout features of brass is its natural corrosion resistance. Unlike carbon steel, which requires protective coatings to prevent rust, brass resists corrosion on its own. This makes brass an ideal choice for hydraulic systems exposed to moisture, chemicals, or other corrosive environments. The ability to resist corrosion ensures the longevity and reliability of the coupling, reducing the need for frequent replacements or maintenance.
Good Machinability
Brass is known for its excellent machinability, meaning it can be easily shaped and fabricated into precise components. This property is particularly beneficial for manufacturing intricate parts like quick couplings, which require tight tolerances and specific designs. The ease of machining brass not only speeds up the production process but also ensures high-quality, reliable couplings.
Durability and Strength
While not as hard as steel, brass is still durable and strong enough for many hydraulic applications. It can withstand moderate pressures and stresses, making it suitable for a wide range of uses. Brass couplings offer a good balance between strength and flexibility, allowing them to endure the mechanical stresses of hydraulic systems without cracking or breaking.
Thermal Conductivity
Brass has good thermal conductivity, which helps in applications where heat dissipation is important. In hydraulic systems, excessive heat can lead to fluid degradation and reduced efficiency. Brass quick couplings can help manage heat effectively, maintaining system performance and preventing overheating.
Compatibility with Fluids
Brass is compatible with a wide variety of hydraulic fluids, including water-based and oil-based fluids. This compatibility reduces the risk of chemical reactions that could degrade the coupling or contaminate the fluid. It also ensures that the coupling maintains its integrity and performance over time, regardless of the fluid used in the system.
Aesthetic Appeal
In some applications, the appearance of the coupling is also a consideration. Brass has a distinctive, attractive appearance that can be a desirable feature in visible or exposed applications. This aesthetic appeal can be important in industries where the visual quality of equipment is as significant as its functional performance.
Cost-Effectiveness
Brass is generally more cost-effective than some other high-performance materials like stainless steel. It offers a good balance of performance, durability, and cost, making it a practical choice for many applications. The relatively lower cost of brass couplings can lead to significant savings, especially in large-scale operations or where multiple couplings are required.
Versatility
Brass quick couplings are versatile and can be used in a wide range of applications, from industrial machinery to plumbing and marine environments. Their ability to perform reliably in various conditions makes them a preferred choice for many engineers and designers.
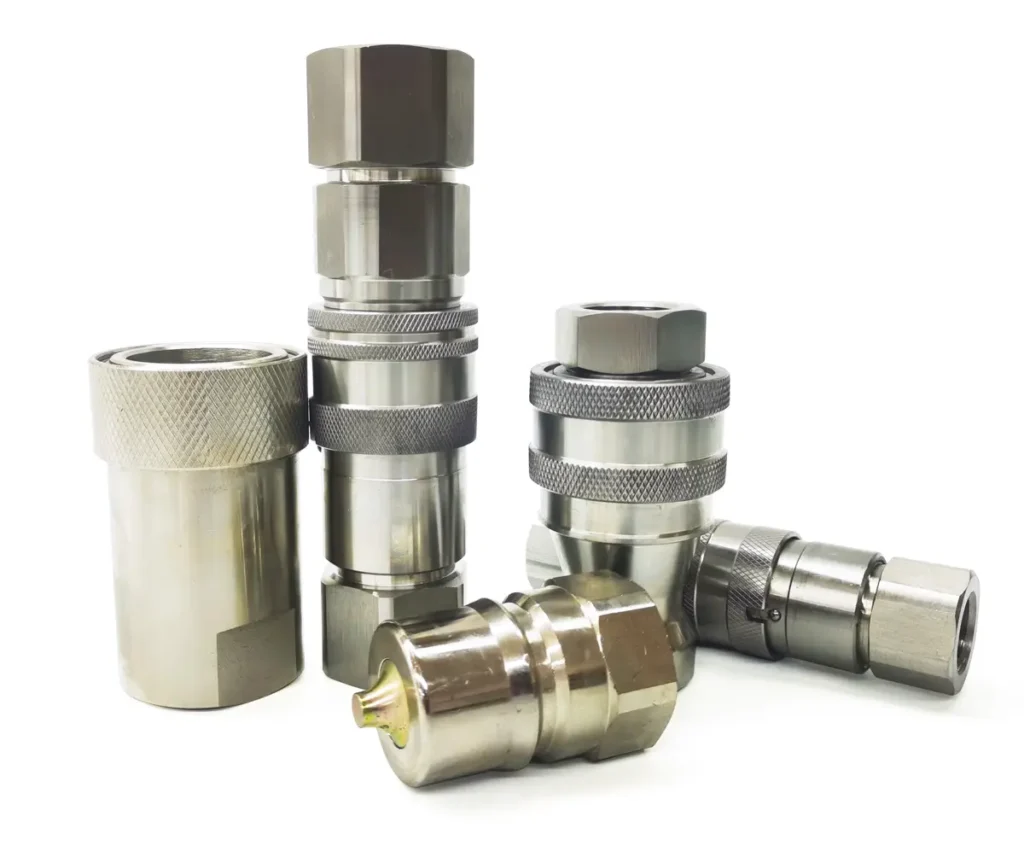
3.Stainless Steel
Stainless steel is an alloy of iron, chromium, and often nickel and other elements, known for its exceptional corrosion resistance and strength. Stainless steel is an outstanding material for quick disconnect couplings due to its corrosion resistance, strength, durability, hygiene, temperature resistance, and aesthetic appeal. Compared with carbon steel quick couplings which are often used in hydraulic systems, stainless steel quick couplings are essential for fluid transfer systems in a wide range of industries.
Why Stainless Steel?
Superior Corrosion Resistance
One of the primary reasons stainless steel is favored for quick disconnect couplings is its exceptional resistance to corrosion. This is particularly important in environments where the couplings are exposed to harsh chemicals, moisture, and extreme temperatures. Stainless steel\’s ability to resist rust and corrosion ensures the longevity and reliability of the couplings.
Strength and Durability
Stainless steel is known for its high strength and durability. This makes it an ideal material for couplings that need to withstand high pressures and mechanical stress. Whether the application involves hydraulic systems or pneumatic systems, stainless steel quick disconnect couplings can handle the demands without compromising performance.
Hygiene and Cleanliness
In industries like food processing and pharmaceuticals, maintaining hygiene is paramount. Stainless steel is non-porous and easy to clean, making it a hygienic choice for quick disconnect couplings. It does not harbor bacteria or contaminants, ensuring that fluid transfer systems remain safe and sanitary.
Temperature Resistance
Stainless steel performs well across a wide range of temperatures, from very low to very high. This makes it suitable for applications that involve extreme temperature conditions. Whether in freezing environments or high-temperature processes, stainless steel quick disconnect couplings maintain their integrity and performance.
Aesthetic Appeal
Although functionality is the primary concern, the aesthetic appeal of stainless steel cannot be overlooked. Its sleek and modern appearance is an added bonus, particularly in applications where equipment visibility is important. Stainless steel couplings provide a professional and polished look.
Types of Stainless Steel Used
Several grades of stainless steel are used for quick disconnect couplings, each with its specific properties:
304 Stainless Steel
304 stainless steel is the most commonly used grade. It offers good corrosion resistance, formability, and weldability, making it suitable for a wide range of applications.
316 Stainless Steel
316 stainless steel provides superior corrosion resistance, especially in marine and chemical environments. It contains molybdenum, which enhances its resistance to chlorides and other corrosive agents.
303 Stainless Steel
303 stainless steel is a free-machining grade that provides good strength and corrosion resistance. It is often used in applications where extensive machining is required.
4.Aluminum
Aluminum is a lightweight metal that offers a good balance of strength, corrosion resistance, and ease of machining. Aluminum quick connectors are not common in our production experience over the past 20 years, because aluminum is not suitable for working under high-intensity working pressure. The so-called aluminum here does not refer to pure aluminum, but aluminum alloy materials. The aluminum alloy quick couplings we encounter now are usually customized products required by customers.
- Lightweight: Aluminum couplings are much lighter than those made from steel or brass, which can be beneficial in applications where weight is a concern.
- Corrosion Resistance: Naturally resistant to corrosion due to the formation of an oxide layer that protects the metal underneath.
- Applications: Commonly used in aerospace, automotive, and other applications where weight savings are essential.
Choosing the Right Material for Your Hydraulic Quick Coupling
When selecting the right material for your hydraulic quick coupling, consider the following factors:
- Environmental Conditions: Determine whether the couplings will be exposed to corrosive elements, extreme temperatures, or high humidity.
- Pressure Requirements: Ensure the material can withstand the operating pressures of your hydraulic system.
- Cost Constraints: Balance the cost of the material with the expected lifespan and maintenance requirements.
- Weight Considerations: For applications where weight is a critical factor, aluminum may be the best choice.
Conclusion
the choice of material for hydraulic quick couplings is crucial for ensuring the efficiency, durability, and reliability of your hydraulic systems. By understanding the properties and applications of carbon steel with zinc or zinc-nickel plating, brass, stainless steel, and aluminum, you can make an informed decision that best suits your specific requirements. Whether you need high corrosion resistance, lightweight construction, or cost-effective solutions, there\’s a material out there that can meet your needs.
Leave a Reply